Roof Drone Inspection Allentown, PA | Drone Roof Leak Detection Services
Proudly serving Pennsylvania and New Jersey for all your commercial or individual aerial needs.
ITC Thermal Imaging Certified, Fully Insured, FAA Licensed
Roof Leak Detection | Infrared Roof Leak Company | Thermal Imaging Services
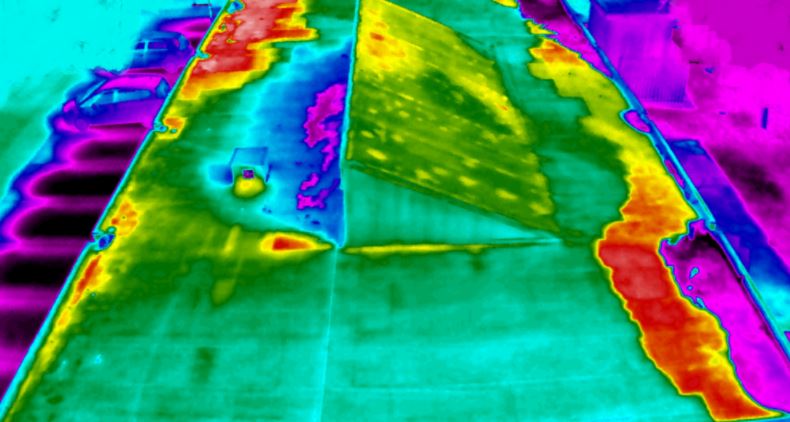
Aerial and Drone Services provides thermal imaging services specific to infrared roof inspections. Infrared roof inspections work best after sunset because the roof releases heat energy that was accumulated over the day. Thermal imaging can detect moisture on a commercial roof without the need to cut it. This technology can save you money and time by providing non-destructive testing options. We offer infrared roofing inspection, infrared testing, roof thermal imaging, and roof moisture surveys for flat roofs. These services are available for Pennsylvania and New Jersey.
We use infrared cameras on our drone fleet to detect thermal leaks. For commercial and residential roofing.
A flat roof leak can cause damage that goes unnoticed for a long time. Water penetrates and soaks into the insulation and decking. The rot can cause costly damage to the roof and can even lead to structural collapse. Thermal imaging cameras have been used by roofing professionals for many years to detect water intrusion and locate moisture below the surface. They also document dryness with precision and confidence. Flat roof membranes act as waterproof barriers between the exterior elements and the inside of buildings. There are many options for their design and materials. They should be capable of expanding and contracting, resisting high winds and solar radiation, and withstanding foot traffic. It’s easy to see how roofs can leak.
A flat roof assembly usually has very little water. Depending on the insulation system used, it is either absorbed or pushed to cracks in the insulation. Water can remain in the roof assembly for a long period of time. Sometimes it even threatens the roof’s life. Thermal capacitance refers to a material’s capacity to store heat. Roof assemblies have a low thermal capacitance in comparison to water. Water needs a lot to raise its temperature, and similarly water must be able to cool down.
Thermal roof inspections are based on the fact that dry roof insulation cools down and heats up faster than wet. Infrared inspection is more than just finding a leak. It also detects the extent of moisture intrusion into the insulation. This can be done by solar heating on a sunny day. After the sun sets, the roof surface cools down at night. The dry roof insulation then cools quicker than the wet. Our technology detects the precise temperature difference.
To obtain excellent infrared images it is important to conduct thermal imaging roofing inspections under the correct conditions. It is important to have a temperature difference between night and day. An infrared image will be produced depending on the type of insulation that’s used to cover a roof. This is indicative of how that insulation absorbs water. Roof insulation that is absorbent acts in a similar way to sponges. Water flows through a roof board by capillary action, before jumping to the next board. This creates a thermal pattern on the checkerboard. When it gets wet, nonabsorbent roof insulation will create a completely different look. Water is not absorbed by the roof boards and flows to the edges. The water collects at the edges of boards, creating a window frame pattern. Other insulating systems may produce different patterns.
Many conditions can create thermal patterns that look like they were made by wet insulation. ASTM C-1153, “Location Of Wet Insulation In Roofing Systems Using infrared Imaging”, suggests that core methods be used to verify the existence of wet insulation.
Thermal imaging cameras are able to create detailed maps of low-slope commercial roofs. They can show where excess moisture is trapped, the source of leaks, and where there is compromised or soaked insulation. The roof is scanned by roofing professionals who take images of the roof to create a composite map or aerial photos of the entire roof. Thermal images are a way to narrow down the search for water intrusion without damaging or puncturing roofs.
Thermal imaging cameras capture infrared radiation. This part of electromagnetic spectrum is invisible to the naked eye. Infrared light can also be used to measure heat radiation from objects. Thermal cameras don’t see visible light so they can measure heat from solid objects like roof membranes or walls.
The technology works on the principle that moisture adds thermal mass (to a roofing material) which allows it to retain heat for longer than the dry material. The thermal camera can capture heat in the same way that normal cameras capture visible sunlight. This creates an image that indicates the extent of moisture problems within the roof system.
The predictive maintenance of roof assets worth millions of dollars is made easier by thermal imaging. It can be used to show moisture infiltration and migration on a roof’s surface. Thermal imaging can help identify roof strengths and ensure long-term conservation. This technology is useful in preventing water damage before it becomes severe. It also allows owners to prevent collateral damage to the interior of buildings. This technology is an additional tool to assess the roof’s overall health without requiring destructive or random testing.
Before thermographic cameras, roofing professionals used other methods to detect leaks and condensation on commercial flat roofs. These methods, including nuclear density gauges and dielectric capacitancemeters, were limited to spot measurements. They also required the collection of roof samples. These technologies were time-consuming, intrusive, and costly guesswork for testing an entire roof. Thermographic imaging, however, is very fast and inexpensive. Infrared light is produced by heat. The infrared light is captured by thermal cameras and taken as a photograph. This is the same process that your smartphone’s camera does for visible light.
The brighter an area is in the final image, the more heat it has. Although thermal cameras create images in black-and-white, thermographers can often add colour to images using computer software. This allows them to emphasize subtle temperature differences.
Certified thermographic professionals use thermographic cameras to detect moisture on roofs. They also take advantage of the fact water adds thermal mass. Roof insulation that is wet absorbs more heat during the day. It releases heat slower at night, making it appear warmer in thermal imaging. Temperature differences between wet and dry roofing materials can only be 2 to 4. This is why it is important for your infrared professional that you know exactly what materials were used in roof construction.
Infrared professionals must wait until the conditions are right to scan the roof. A thermographer can choose between a hot or cold scan depending on the weather and climate conditions. It is also not recommended that you scan your roof after it has been wet from rain. It will be difficult or impossible to determine if the moisture detected on the scan is rainwater or from a leak if the roof is damp from rain. Dew is the same. It is difficult to distinguish between internal and external condensation once the dew point has been reached.
The scan can be done in the evening as long as it is dry and warm. The roof will start to lose heat as the temperature drops at night. If it does not, it should be restarted another night.
A thermographer with experience can help you choose the right climate for you, regardless of your climate.
A wide-angle lens with high spatial resolution is also important. This allows for images that not only show the moisture but also enough of the roof so that roofing professionals can use them to pinpoint the location.
The advantage of taking thermographic images from a higher position is that they can capture more of the roof’s surface and any landmarks that could be used to aid in repair. This method prevents thermographers from taking photos too close to wet areas.
Thermal footage can be taken from an aircraft or drone. This has many benefits. This method allows the roofer to create a complete map of a roof. These maps can be extremely detailed with a high-resolution thermal cam. A powerful thermal camera is required, because the heat dissipates faster the farther you are from the roof’s surface. This makes readings more difficult.
For roofs that are difficult to access, very dangerous or extremely large, aerial thermal roof measurements might be the best option. An aerial scan is more convenient for roofers because they can inspect multiple roofs at once and don’t need to transport their equipment. This type of scanning was previously very expensive, but drone technology makes it much more affordable.
Before you can conduct these scans, your thermal imaging professional must inspect the roof for any access points, heat sources, flashing, penetration details and safety hazards. This will allow the thermal professional to interpret the final results more accurately and help to ensure safety while performing the scan.
Even if the roofs appear to be functioning normally, building owners will reap the benefits of regular thermal imaging roof inspections. A baseline thermal signature is useful for budgeting and long-term maintenance planning. The use of imaging can help with building heat/cooling projections, as well as planning for long-term thermal differentials or loading. Conservationists can help identify roof components that are not performing and return insulations’ R-values to their original condition.
Infrared roof inspections provide valuable diagnostic information that can be used to plan capital budgets, develop a roof maintenance program and make informed decisions about roof repairs, replacement, or resurfacing using one of the most popular roof coatings.
Water can enter a roof via cracks in the waterproofing layer (s), deterioration, tears or seams. This causes the insulation to trap moisture and cause it to leak. Because wet insulation is less resistant to heat than dry, it causes energy loss. Water can get into the interior of the building, causing structural damage and productivity loss. If the concrete deck is not maintained in good condition, it absorbs water and the wood deck or metal decking components will rot.
The sun’s energy is reflected onto the roof during the day and into the substrate. At night, the roof heats up and radiates it back into space. Radiational cooling is the term for this phenomenon. The roof’s areas of higher mass (wet) will retain heat for longer than the ones of lower mass (dry). Infrared imaging can detect heat and “see”, the warmer, higher-mass areas during the “window of uneven heat dissipation”. You can also perform heat loss and other IR services simultaneously.
You, whether you’re an investor, a seller, a roofing company, facility manager or facility manager, it is important to identify moisture and heat loss issues in your roof when assessing maintenance requirements and building values. To avoid blistering, a roof must be completely dry before applying a new roofing coating.
Are you a homeowner with a huge roof, such as a school campus, apartment complex or shopping center? You can see trapped moisture on large roofs best from the air!
Are you thinking of installing solar panels Are you sure your roof is dry? Infrared roof moisture inspections are a great way to ensure that solar panels are not mounted on roofs with trapped moisture. Solar Panel infrared thermography is the best method to detect trapped moisture on flat roofs with 100 percent coverage. A PV solar panel array’s life expectancy can range from 15-20 years. Latent moisture problems on a roof may need to be addressed immediately after installation. It is best to not discover roof moisture problems after solar panels have been installed. The cost to remove solar panels to fix a roof that is wet will increase, as well as the loss of power/revenues and potential damage to the panels and electrical connections. If the panels are removed and reinstalled following installation, there could be problems with the warranty.
It is essential to know the condition of your roof before you have solar panels installed. If the installer of the solar panels is not certified infrared inspector, we recommend that they inspect your roof before you install them. To ensure that your roof is ready for solar panel installation, hire a professional infrared inspection firm.